
Product manufacturers across categories like household chemicals, cosmetics, pharmaceuticals, and food and beverage industry play an increasingly important role in meeting consumers’ changing needs and values. They need to ascertain that their products reach their consumers in top condition. Poor merchandise state such as leaking and damaged containers, spoiled and contaminated products are major complications that put safety at risk.
Thanks to worldwide application knowledge and the most advanced production techniques, the ability to realize a perfect seal every time is now achievable.
The use of the induction sealing system, when properly applied, can enhance the value of the product. By making the container airtight (hermetic), it provides a tamper proof seal that prevents all the above mentioned problems while maintaining a professional overall look. The induction sealing system is also ideal to extend product shelf life and to preserve freshness that fosters consumer confidence.
What to look for in an Induction Seal:
- A good seal is achieved within minutes of the induction sealing process. For total sealing – induction foil manufacturers highly recommend 24 hours before the best end result is achieved
- Over Heating – Pay attention to any signs of scorching or melting inside the cap
- Under Heating – if the foil sealing layer did not melt and bond with the entire rim of the bottle or jar top neck surface.
- Proper Heating – is determined if the foil totally seals around the rim of the product and secondary cap lining materials, the bottle neck and the cap are not overheated.
- An experienced operator will know how warm a bottle lid should get before it starts to cool.
- An experienced eye will pick symmetric heat patterns in the induction foil and in foam backing material behind some induction foils
Proper Induction Sealing is met if:
- For non breakable containers, the seal can usually stand the force of dropping without the cap.
- For easy-peel seals, the seal can be taken off without leaving behind a foil ring. For permanent weld seals the foil will need to be cut.
- No leak after being dropped
How to achieve a perfect induction Seal?
To realize a consistent product seal, container, cap closure, lining material, and induction sealer should be well matched. To find the right combination, we recommend that you consult with your cap closure lining material supplier or Induction Sealing equipment supplier. To record the energy transfer window for good sealing results we recommend and supply the Linepatrolman™.
Container
The majority of induction sealed containers are plastic, however, glass containers can be induction sealed too –
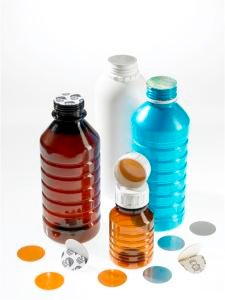
usually for dry products like coffee. The choice of container type is made based on the product compatibility, marketing and logistic considerations.
Cap Closure
The cap closure needs to have a flat inside area to hold an induction liner. Screw on caps allow for a wider range of hard and soft cap lining materials. Snap on caps are generally more suited to softer cap lining material. If using a two part induction sealing material where a foil separates from a backing material, the cap may need to have features that retain the backing material when the two part induction material separates as the container is opened.
Lining Materials
The determination of the appropriate induction seal material is dependent on the following:
- What the container is made of
- Product content
- Duration of usage
- Cap Tolerance any Type (eg Screw on or Snap on caps)
- Method for which the lining material will be inserted into the cap
Induction Sealer
Choosing the right machine for your needs is an important task. In determining the right supplier, be sure that they:
- The supplier can offer technical advice on the induction sealing process and if necessary participate in the closure and container development side of things where necessary.
- The supplier of the machinery either supplies or can also advise on the supply for the induction lining material.
- The supplier ONLY provides CE safety certified equipment. Induction sealing equipment involves very high electric currents and electromagnetic fields. Places like China and India are producing and supplying very low cost options WITHOUT CE certification.